Have any questions?
+44 1234 567 890
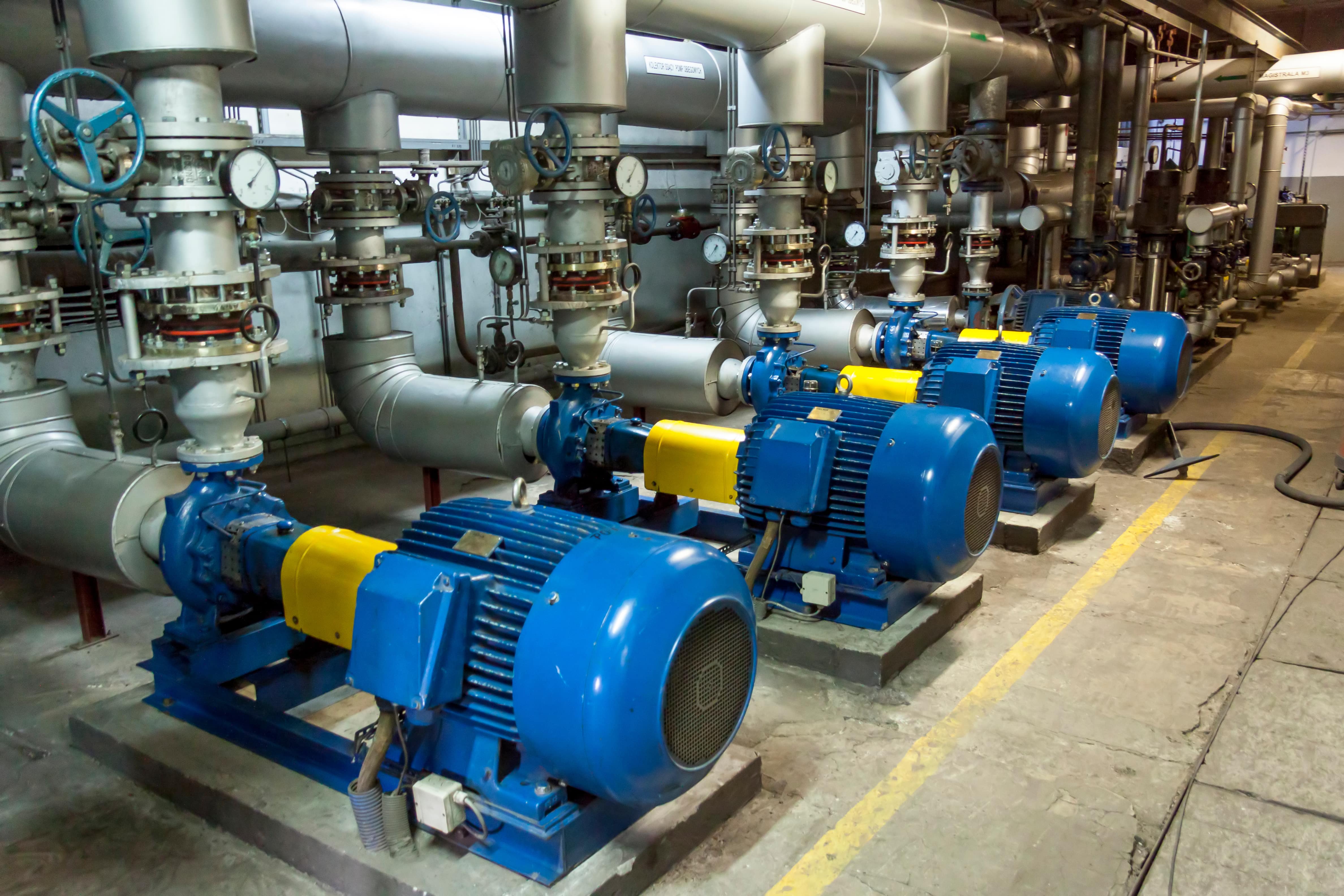
Pumpentechnik Projektierung: Effiziente Lösungsansätze für Ihre Bedürfnisse
Warum professionelle Projektierung entscheidend ist
Fehlausgelegte Pumpen verursachen Energieverluste, Kavitation, überhöhten Verschleiß und ungeplante Stillstände. Eine strukturierte Projektierung von Pumpentechnik stellt sicher, dass Hydraulik, Werkstoffe, Antrieb und Regelung exakt zum Medium, Lastprofil und Lebenszyklusziel passen – und zwar herstellerunabhängig.
Schritt 1: Präzise Bedarfsermittlung
Wir erheben alle relevanten Parameter: Fördermedium (Chemie, Feststoffanteile, Abrasivität, Rheologie, Temperatur, pH), Fördermenge (Min/Max/Regelbereich), Förderhöhe / Druckstaffelung, NPSH-Verhältnisse, Pulsations-/Schwingungsanforderungen, Redundanz (1+1 / N+1), Betriebsmodi (Batch vs. kontinuierlich), zukünftige Skalierung. Ergebnis: belastbare Last- und Betriebspunkte.
Tools: Betriebspunkt-Spreizung, Lastkollektive, Lebensdauer‑/MTBF-Ziele, Risikomatrix.
Schritt 2: Hydraulische & mechanische Auslegung
Auswahl geeigneter Pumpenbauarten (Kreisel-, Seitenkanal-, Verdränger-, Schrauben-, Kolben‑, Membran-, Dosier-, Magnetkupplungs-, Tauch-, Vakuum- oder Spezialpumpen) anhand Effizienzkennfeld, Kennlinienform, Feststofftoleranz, Pulsation, CIP/SIP-Fähigkeit. Optimierung auf Best Efficiency Point (BEP) bei typischer Last, Minimierung von Teillast-/Überlastbetrieb. Mechanische Aspekte: Wellen- & Lagerdimensionierung, Dichtungskonzept (Gleitring einfach/doppelt, Cartridge, Stopfbuchse), Werkstoffpaarungen (z. B. Duplex, Hastelloy, gehärtete Legierungen, Elastomere).
Schritt 3: Werkstoff- & Korrosionskonzept
Chemische Beständigkeit, Spalt- & Lochkorrosion, Erosionsneigung, Temperaturwechsel, Hygieneanforderungen bestimmen Materialwahl für Gehäuse, Laufrad/Rotorelemente, Wellen, Dichtungen, O‑Ringe. Ziel: Maximierung der Standzeit und Minimierung ungeplanter Dichtungswechsel.
Schritt 4: Antriebs- & Regelstrategie
Frequenzumrichter (Drehzahlregelung), Softstart, Lastmanagement (Multi-Pumpen-Verbund, Master/Slave, Duty/Stand-by), Energie- und Kennlinienoptimierung (Q-H-Kennfeld-Anpassung, Laufradbeschneidung, Bypass-Minimierung). Betrachtung von Teillastwirkungsgraden, Anfahrstromreduktion, ggf. IE5/PM‑Motoren. Integration in SPS/Leittechnik via gängige Kommunikationsprotokolle.
Schritt 5: Systemintegration & Peripherie
Rohrleitungsdesign (Strömungsgeschwindigkeit, Druckverluste, Kavitation), Armaturen (Absperr-, Regel-, Rückschlag-, Sicherheitsventile), Filter/Siebe, Sperr- und Spülsysteme, Entgasung/Entlüftung, Auffang- und Sicherheitswannen, Vibrationsentkopplung, Mess- & Regeltechnik (Durchfluss, Druck, Temperatur, Füllstand, Schwingung, Leckage), EMV-gerechte Verkabelung.
Schritt 6: Digitalisierung & Condition Monitoring
Sensorik für Schwingung, Lager-/Dichtungstemperatur, Motorstrom, Differenzdruck, Leckage. Datenaggregation in Edge-/Cloud-Systemen, Trendanalysen, Alarmgrenzen (Predictive Maintenance). KPI-Dashboards (Energie kWh/m³, MTBF, Verfügbarkeitsrate) schaffen TCO-Transparenz.
Schritt 7: Dokumentation & Compliance
Technische Datenblätter, P&IDs, 3D-/Isometrien, Schaltpläne (EPLAN), Werkstoffzeugnisse, Prüf- und Abnahmeprotokolle, ATEX-/Druckgeräterichtlinie (falls relevant), Betriebs- und Wartungsanleitungen. Lückenlose Dokumentation erleichtert Zulassungen, Audits und späteres Retrofit.
Effizienz- & Nachhaltigkeitshebel
Hebel | Wirkung |
---|---|
Drehzahlregelung | Reduziert Energieverbrauch bei variabler Last |
Optimierter BEP-Betrieb | Minimiert Verschleiß & Kavitation |
Doppelte Gleitringdichtung bedarfsgerecht | Senkt Medienverlust & Ausfallrisiko |
Werkstoffoptimierung | Verlängert Standzeiten, reduziert Ersatzteile |
Mehrpumpen-Justierung | Gleichmäßige Laufzeitverteilung / Lebensdauer |
Condition Monitoring | Frühwarnung statt Schadensstillstand |
Rohrleitungsoptimierung | Geringere Druckverluste, kleinere Antriebe |
Typischer Projektablauf
-
Kick-off & Datenaufnahme
-
Analyse / Betriebspunktdefinition
-
Varianten- & Wirtschaftlichkeitsvergleich (Invest / Energie / Wartung)
-
Detailengineering (Hydraulik, Werkstoffe, Steuerung)
-
Fertigung / Beschaffung / Vormontage
-
Installation & Ausrichtung / Spül- & Drucktests
-
Inbetriebnahme / Performance-Test / Abnahme
-
Schulung & Übergabe an Service (Wartungs- & Monitoringkonzept)
Praxisnutzen für Ihr Unternehmen
-
Energieeinsparung: Optimierter Wirkungsgrad, bedarfsgerechte Regelung, geringere spezifische kWh/m³.
-
Verfügbarkeit: Zustandsüberwachung, redundante Konzepte, planbare Wartungsfenster.
-
Kostenkontrolle: TCO-Transparenz (Invest, Betrieb, Wartung, Ersatzteile), reduzierte Stillstands- und Dichtungskosten.
-
Sicherheit & Compliance: Richtlinien- und Normkonformes Design (z. B. ATEX, Druckgeräte), dokumentierte Prüfungen.
-
Skalierbarkeit: Reserven für zukünftige Volumen- oder Druckerhöhungen, modulare Pumpenfelder.
-
Nachhaltigkeit: Längere Standzeiten, geringerer Energie- und Ressourcenverbrauch.
Planen Sie eine neue Pumpenanlage oder möchten bestehende Systeme energetisch und betrieblich optimieren? Fordern Sie jetzt eine herstellerunabhängige Projektierungsanalyse an – mit belastbarem Varianten- und TCO-Vergleich.